كيف يمكن تقليل التكاليف خلال أزمة كوفيد-19 من خلال التعبئة المستدامة
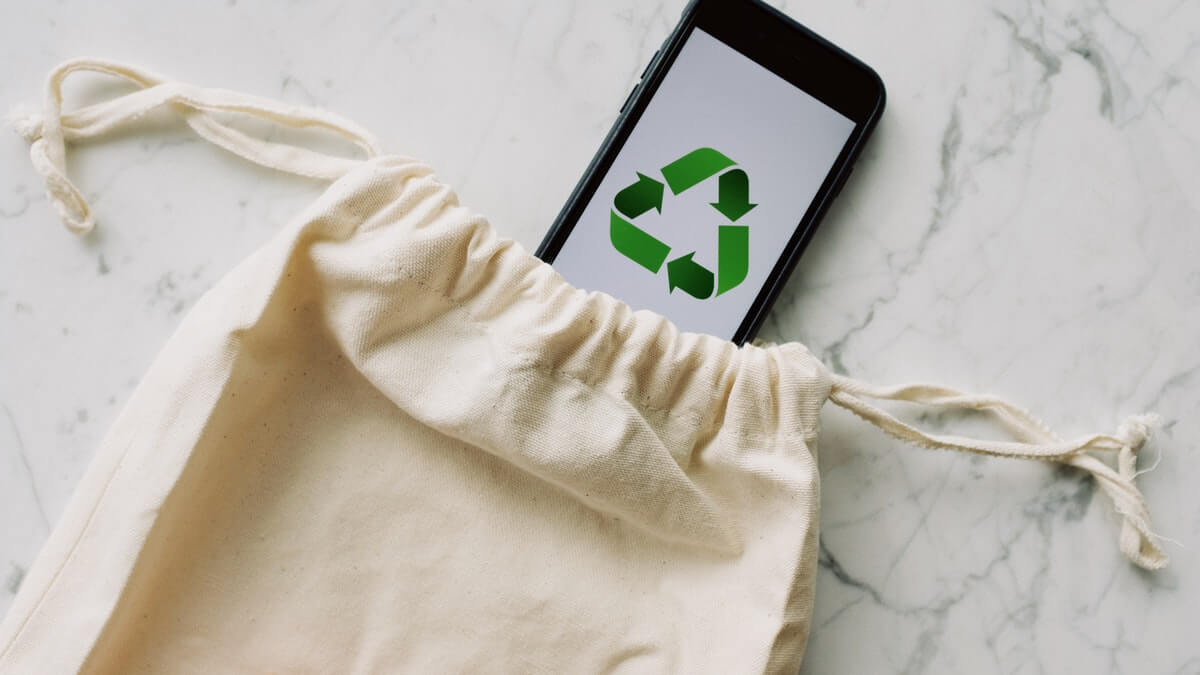
كيف يمكن تقليل التكاليف خلال أزمة كوفيد-19 من خلال التعبئة المستدامة
The need for enterprises to be more efficient could have not been more relevant than it is today, thanks to the huge costs imposed by the COVID19 pandemic. One of the ways in which enterprises that manufacture consumer goods can reduce their costs is by reducing wastage in packaging. With intelligent innovation, it is possible for enterprises to combine economic efficiency with compliance with health and hygiene requirements in packaging to achieve the best of both the worlds. Packaging that entails the reduction of wastage and seeks to enable enterprises to do more with less creates new avenues for cost reduction while ensuring hygiene factors for contactless delivery. Some of the major ways in which packaging can enable such hygiene centric cost reduction are as follows:
Reimagine Packaging Design for E-Commerce and Contactless Deliveries
Give the need for social distancing in the wake of the COVID19 pandemic, a clear trend that is emerging in the consumer packaged goods industry is a shift of consumers away from supermarkets, malls, and grocery stores and towards e-commerce enterprises that offer contactless delivery of goods. As such, the paradigm on which packaging is designed has shifted from the locus standi of store shelves to that of e-commerce and online retail. This implies that manufacturers of consumer packaged goods need to pivot their packaging design for greater and clearer visibility on personal devices like smartphones and tablets rather than store shelves. Doing so can actually allow enterprises to reduce packaging costs by forgoing the packaging requirements of grocery stores and supermarkets.
Vendor Consolidation and Single-Window Approach to Procurement of Packaging
Given the evolving contours of quarantine and lockdown across diverse geographies and the decentralized regulatory environment governing these, it makes enormous good sense to suggest that enterprises shall do well to focus on a single-window approach for the procurement of packaging materials to reduce the risks and costs associated with disruptions and freezing of local logistics. An integrated platform for sourcing packaging materials from a single vendor with strong upstream partnerships with local MSMEs and logistics service providers can enabler manufacturers to reduce costs, TAT and respond swiftly to market demand in niche markets.
Digitization of Packaging Supply Chain to Enable Mapping of the Demand and Supply Gap
One of the major factors affecting the packaging supply chain is the manual workflow that impairs the optics of vendor KPIs for packaging. A switch to digital packaging supply chain platforms can enable enterprises to map supplier capacity, objectively assess the TTR (time to recover) from lockdowns, and consequently quantify the quality, cost, and delivery metrics. This shall further allow enterprises to make their packaging supply chains faster, safer and more de-risked during the COVID19 pandemic and beyond.
Differentiate the Necessary Costs from the Unnecessary Costs in Design
The best packaging designs that lead to cost reduction follow a 4D Methodology of ergonomics, cost, sustainability, and logistics. If you want to bring down costs without impacting performance, then you need to think about how you can curb costs on aesthetic aspects. You can do in-depth scrutiny of the below questions to enable the best possible cost optimization process within each carton:
- Can your printing cost be optimized to highlight essential information only?
- Do you need full-color printing? Are there any design tweaks that can give coverage to the blacks and whites?
- Does your product need an inner pack and an outside carton?
- Can your packaging material have more environment-friendly materials like jute, which can reduce your carbon footprint?
Use of Technology to Optimize Packaging Costs
Brands are increasingly using popular CAD systems like Solidworks, Siemens NX12, and ArtiosCAD to ensure the right size and strength needed to package a product. Such technologies will help your enterprise to figure out a lot of information like:
- Dimensions of the inner pack and outer cartons
- Use of right packaging design like blisters, clamshells, corrugated boxes, paper packaging, sacks, or boxboards
- Use of the right dunnage material and size for full protection of the product throughout its journey to the end customer
- How does the carton need to be stacked on a pallet to enable maximum cartons shipped per pallet and higher pallet density?
- Configuration for loading container that holds the pallets
With a focus on these factors in packaging, supply chain professionals can effectively protect the product during its shelf life and the integrity of the contents inside the package. As a result, enterprises gain from reduced cost benefits like no product re-work, lower returns and replacements, and higher savings due to lower occurrence of damaged goods or ‘written off stock’. Also, shipping costs reduce because enterprises can do away with dead weight and optimize volumetric weight and thus make their supply chain more efficient.
Ergonomic Pallet Redesign
Companies are also looking to reconfigure the labor aspect involved in the ‘per piece’ packaging with compact packaging. This technique of simplifying the packaging process needs less labor and brings down the amount of warehouse space needed for storage. Such innovation helps the brand redesign pallet configuration and ship more product volume per pallet. Take the case of an online home décor brand, Exclusive Lane. They used India Post for delivery services. But this service stipulated the wrapping and stitching of products in jute. This step not only took 2 to 3 hours but also an additional cost to execute. When they changed the delivery service, they were able to do away with this packaging cost overhead.
What is Good for Unit Economics Can Address Hygiene Factors Too
It is apparent that in the wake of the COVID19 pandemic enterprises across a wide spectrum of industry verticals will have to prioritize hygiene even as they continue to explore new ways to lessen the devastating impact of COVID19 on businesses. Even a 1-3% cost reduction assumes importance in this context and sustainable packaging has the potential to create new avenues of cost efficiency for enterprises. As enterprises stare at a new normal characterized by the need to be more efficient, safer, and faster in their supply chains, the shift will transform from a trend to a mainstream practice in the packaging domain. In doing so, they are also managing to bring down costs and improve toplines, as seen in the above examples.
كوفيد-19: المراحل الثلاث للإصلاح في مجال التصنيع.
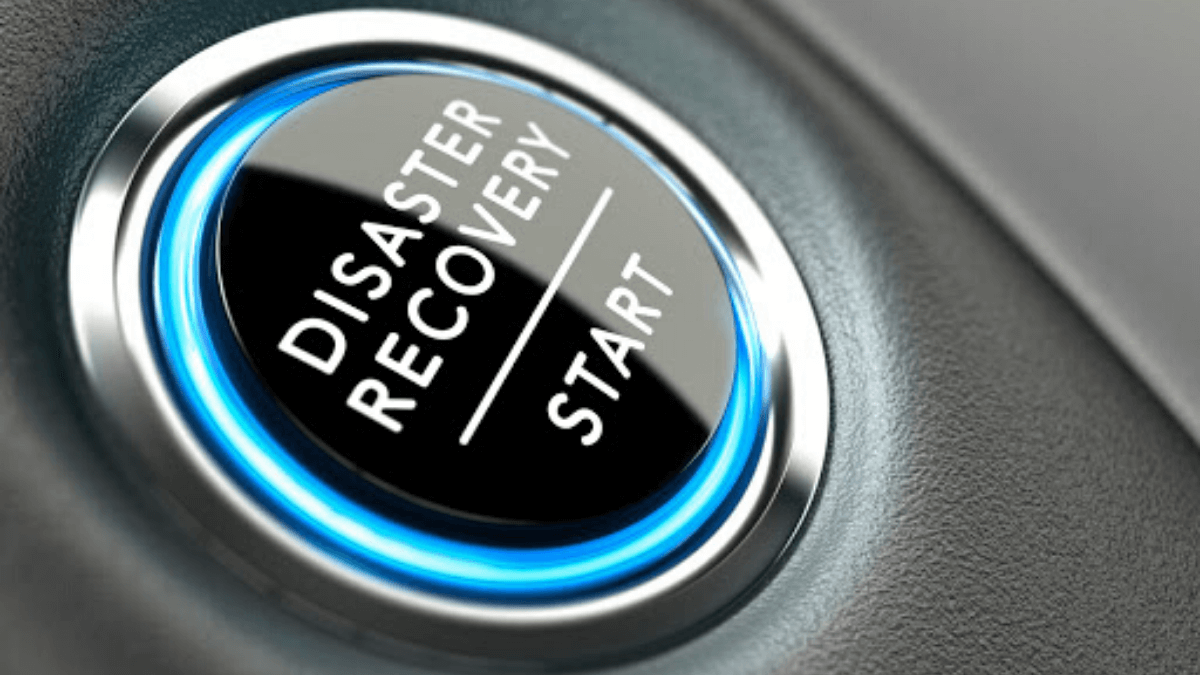
كوفيد-19: المراحل الثلاث للإصلاح في مجال التصنيع.
How badly has the manufacturing sector been hit by the COVID19 pandemic? Is recovery from the current situation even possible? Given the huge costs imposed by the lockdown and the unpredictable contours of the spread of the contagion, what can manufacturers do to resume their business once the first signs of ‘Unlock 1.0’ are visible? If so, what trajectory will enterprises in manufacturing need to take to make up for the significant losses that have already occurred and the ones that are anticipated to emerge over a period of time?
The United Nations (UN) has projected that the global economy will shrink by 3-4% in the year 2020. As an outcome, manufacturing enterprises need to introspect on the steps that they need to take today, tomorrow, and over the course of time, leading into the future of a post-pandemic world. At Moglix, we believe that enterprises need to visualize the road to recovery by first rebuilding trust today, enabling businesses processes with technology for tomorrow, and building futuristic supply chains using advanced technology for the foreseeable future beyond COVID19.
What Manufacturers Need to Do Today?
Rebuilding Trust: The Great Lockdown in 2020 has lent a major shock to public healthcare systems and has created an enormous trust deficit at both individual and institutional levels. In the manufacturing sector, trust erosion has emancipated in many forms, including withdrawal of labor from participation in production processes, opaqueness in supplier collaboration, and a lack of visibility into insights on key performance indicators of cost, quality, and expected timelines of delivery. As such decisions to deploy resources and engage them into manufacturing during ‘Unlock 1.0’ must be pivoted on addressing the trust deficit secularly first within enterprises and then scaling up across all enterprises constituting the supply chain in the manufacturing sector.
- Ensuring Health Protection: At the enterprise level, this calls for ensuring the availability of quality rated personal protective equipment (PPE) kits, and medical kits for all employees and the creation of fool-proof systems for implementation of standard operating procedures for regular sanitization of the physical environment at the workplace. The second imperative is to ensure transparency in sharing information on the deployment of such social distancing and contact tracing measures on a “need to know basis” among all stakeholders in the supply chain while staying within the ambit of data privacy.
- Fixing the Broken Fragments with Data: Reviewing supplier collaboration and manufacturing workflows today will play a huge role in creating an open and transparent dialog among OEMs, CMs, EPC enterprises, MSMEs, and suppliers across multiple tiers in the supply chain. A pilot project for mapping the supplier network can follow a template similar to the one used by bankers to conduct a stress test of debtors during the Great Meltdown of 2007 and focus on three Cs: character, capability, and credibility. One way to do this is by creating a similar stress test in manufacturing and encompassing the three Cs can be of paramount importance:
- What is the site location of the supplier including the city, region, and country? Do we have insights into the real-time status of COVID19 spread there?
- Is the supplier adhering to social distancing and contact tracing practices to steer clear of COVID19 risks?
- What are the parts procured from this site? What is the part number and description, part cost, annual volume for this part, rate of replenishment of inventory for this part, and the total spend (per year) from this site?
- What is the end product including the OEM’s end product(s) that uses this part? What is the profit margin for the end product(s)?
- What are the lead times from the supplier site to OEM sites in days?
- What is the Time to Recovery (TTR)? What time would it take for a site to be restored to full functionality if the supplier site is down, but the tooling is not damaged or if the tooling is lost?
- What is the cost of loss if expediting components from other locations is possible? If so, at what cost?
- Can additional resources (overtime, more shifts, alternate capacity) be organized to satisfy demand? If so, what is the cost?
- Does the supplier produce only from a single source? Could alternate vendors supply the part? Is the supplier financially stable? Is there variability in performance (lead time, fill rate, quality)?
- What are the mitigation strategies for this supplier-part combination? Who are the alternate suppliers? How to arrange excess inventory?
What Manufacturers Need to Do Tomorrow?
Enabling Business Processes with Technology: As enterprises in manufacturing and supply chain operations look to move beyond the immediate impact of the COVID19 pandemic over the next financial quarter, it shall make sense for them to scale up the best practices from the peak of the recessionary phase and integrate siloed data repositories for multiple functions into a compact source to pay (S2P) platform for a single-window approach to manage approvals and authorization for procurement decisions. This shall serve the purpose of augmenting enterprise-wide transparency and building greater efficiencies by facilitating multi-tenant models for collaboration spanning across the nerve center leadership, customer relationship, and supply chain teams to optimize costs. Small steps towards instituting a digital “cost control tower” to prioritize urgent and important payments and define clear reporting metrics for managers to track the liquidity status in real-time may over the period of the next financial quarter evolve into rolling forecasts to identify major areas of EBITDA risks and finally implement zero-based budgeting (ZBB) to achieve greater fiscal prudence for discretionary expenditures and indirect procurement. Authorization and access to such information systems may slowly be devolved amongst mid-level managers to move the enterprise forward along the lines of supply chain digitization and learning curve from a strategic to a tactical level
What Manufacturers Need to Do in the Future?
Build Futuristic Supply Chains using Advanced Tech: One of the major lessons coming out of the COVD19 pandemic for enterprises in manufacturing shall be gaining visibility into the next steps and future-proofing their supply chains. They will have learned the value of anticipating the next supply chain disruption in advance and adjusting their positions in the market while they still have time to do so.
Using Advanced technologies like contract management and predictive analytics that allow enterprises to stay informed on their supplier relationships, map the contributions of suppliers by value and volume, and assess their exposure to volatile business environments are likely to emerge as the enablers of de-risking supply chains. With AI, ML, and advanced analytics being able to capture deeper insights on the next steps in the supply chain right up to the end consumer, the direction of supply chain automation is likely to direct towards demand-driven planning and forecasting (DDPF).
While temptations to stay in denial of the challenges in a post COVID19 world and to retain the status quo may still be strong, enterprises shall do well not to risk a return to pre-COVID19 coordinates of workflow, collaboration, and distribution. Instances such as the Y2K, the subprime crisis of 2007, and climate change should serve an adequate warning to enterprises to steer clear of the lure of wishing away a rebound of challenges and then waking up to grave realities. A future that is driven by a high degree of technology enablement for information sharing, engaging in transparent dialogs to drive outcomes, and creating coordinated responses to a crisis may present us with a vertical upward shift in costs. Irrespective of how steep the shift in costs may be, it shall be prudent for enterprises to believe that they shall be able to pass on such incremental costs of technology enablement across the downstream of the supply chain right up to the end consumer.