Identifying and Eliminating Waste in Warehouse Operations
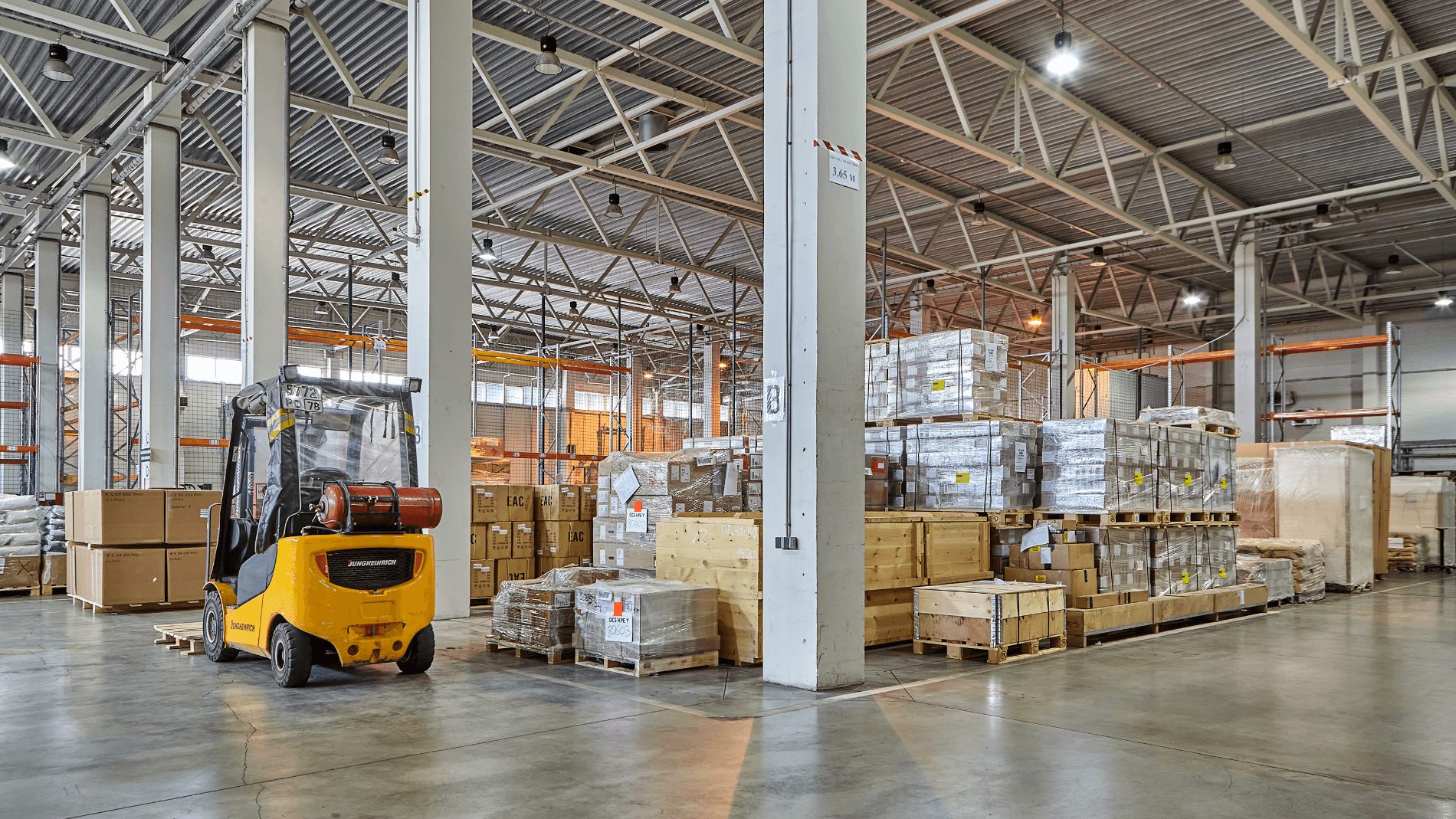
Efficiency and cost savings are critical goals for any warehouse operation. To achieve these objectives, it is essential to identify and eliminate waste within warehouse processes. According to a study by the Warehousing Education and Research Council (WERC), transportation waste accounts for an average of 30% of total logistics costs in warehousing operations. Waste can manifest in various forms, hindering productivity, increasing costs, and impacting customer satisfaction. In this blog post, we will explore different types of waste commonly found in warehouse operations, discuss their impact, and share relevant statistics to emphasize the importance of waste elimination. By understanding and addressing these waste types, businesses can enhance operational efficiency, reduce costs, and optimize their warehouse operations. The Institute of Industrial Engineers (IIE) states that reducing waste in warehouse operations can lead to cost savings of up to 20% and productivity improvements of 10-30%.
Types of Waste in Warehouse Operations:
Transport Waste
Transportation waste refers to inefficiencies in the movement of goods within the warehouse. An example of this could include unnecessary material handling, inefficient routing, and excessive travel distances. These waste factors can result in increased fuel consumption, higher transportation costs, and delays in order fulfillment.
To eliminate transportation waste, warehouse managers can implement strategies such as optimizing delivery routes, consolidating shipments, and utilizing software solutions for route planning and tracking. By doing so, businesses can reduce fuel consumption, transportation costs, and improve overall delivery efficiency.
Inventory Waste
Inventory waste arises from poor inventory management practices. Overstocking, underutilization of available space, and the presence of obsolete inventory can tie up capital, lead to storage inefficiencies, and increase the risk of product expiration or obsolescence.
To address inventory waste, warehouse managers can focus on implementing just-in-time inventory management techniques, conducting regular inventory audits, and utilizing data-driven forecasting models. These strategies help optimize inventory levels, reduce carrying costs, and improve space utilization within the warehouse.
Motion Waste
Motion waste encompasses unnecessary or excessive movements within the warehouse. N example of this can include inefficient picking routes, disorganized storage layouts, and excessive searching for items. Motion waste contributes to increased labor costs, reduced productivity, and longer lead times. The Lean Enterprise Institute found that motion waste can contribute to up to 50% of total labor time in some warehouses, indicating significant room for improvement.
To eliminate motion waste, warehouse managers can optimize the layout of the warehouse, streamline picking paths, and implement efficient storage systems. Leveraging technology solutions like barcode scanning and automated guided vehicles (AGVs) can further enhance efficiency by minimizing unnecessary motion and improving overall productivity.
Waiting Waste
Waiting waste occurs when there are delays or bottlenecks in warehouse processes. It can be caused by factors such as lack of coordination between departments, machine breakdowns, or inadequate staffing. Waiting waste leads to idle time, decreased throughput, and customer dissatisfaction due to delayed order fulfillment.
To address waiting waste, warehouse managers should focus on improving communication and coordination between teams, ensuring machinery is well-maintained and properly serviced, and
optimizing staffing levels based on demand. By minimizing waiting times, warehouses can enhance overall productivity and improve customer satisfaction.
Overprocessing Waste
Overprocessing waste arises from unnecessary or excessive steps in warehouse operations. This can include redundant paperwork, double-checking processes, or additional inspections beyond what is required. Overprocessing waste adds complexity to operations, increases costs, and hampers overall efficiency.
To eliminate overprocessing waste, warehouse managers should review and streamline existing processes, automate repetitive tasks where possible, and ensure that quality checks are performed at appropriate stages. By eliminating unnecessary steps and optimizing processes, warehouses can reduce costs, improve operational efficiency, and accelerate order fulfillment.
Defects and Rework Waste
Defects and rework waste result from errors or substandard quality in warehouse operations. This includes damaged goods, incorrect labeling, picking errors, or inadequate packaging. Defects and rework waste lead to customer dissatisfaction, increased costs, and loss of productivity. The National Association of Manufacturers (NAM) reported that defects and rework waste can account for up to 20% of overall production costs in warehouses
To address defects and rework waste, warehouse managers should focus on implementing quality control measures, providing adequate training to warehouse staff, and utilizing technology solutions such as automated picking systems or quality assurance software. By improving accuracy and minimizing errors, warehouses can reduce rework, enhance customer satisfaction, and increase operational efficiency.
Every warehouse is unique, and identifying specific areas of waste requires a thorough analysis of your own operations. Tailor the waste elimination strategies to suit your warehouse’s specific needs and continually strive for continuous improvement to maximize efficiency and achieve long-term success. To successfully eliminate waste, warehouse managers should adopt a systematic approach that includes analyzing current processes, identifying areas of waste, implementing appropriate strategies, leveraging technology solutions, and continuously monitoring and improving operations. By embracing lean principles and utilizing data-driven insights, businesses can create leaner and more efficient warehouse operations, resulting in cost savings, improved customer experiences, and a competitive edge in the market. Moglix’s evolving warehouse network in UAE is providing reliable inventory management solutions to its customers. With strategically located warehouses in the UAE, Moglix ensures quick and efficient delivery, reducing lead time and optimizing supply chain management. Know More